Qu’est-ce que l’Industrie 4.0 ?
L’industrie 4.0 : que se cache-t-il derrière ce titre emphatique ? Pourquoi l’Internet des Objets (IoT) révolutionne-t-il l’univers industriel ? La conférence « SNCF et l’IoT – Décryptage » qui s’est tenue le 23 septembre au 574 de Saint-Denis proposait une introduction au sujet, résumée ici pour vous.
Publié le
Par La Redaction
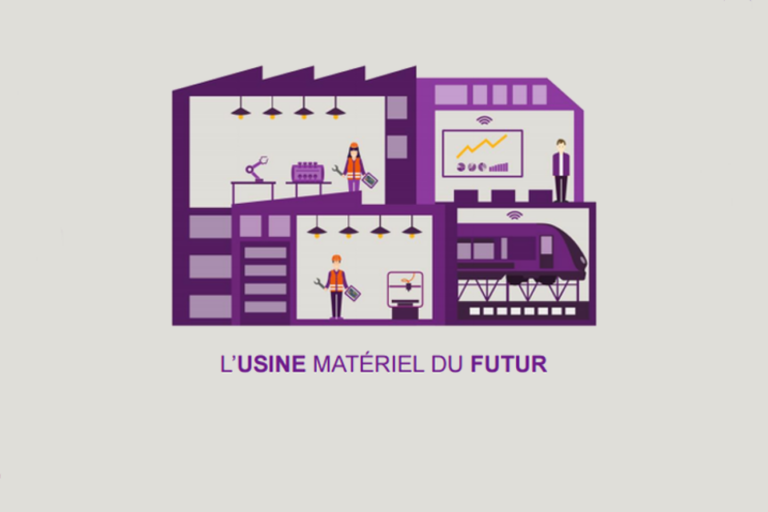
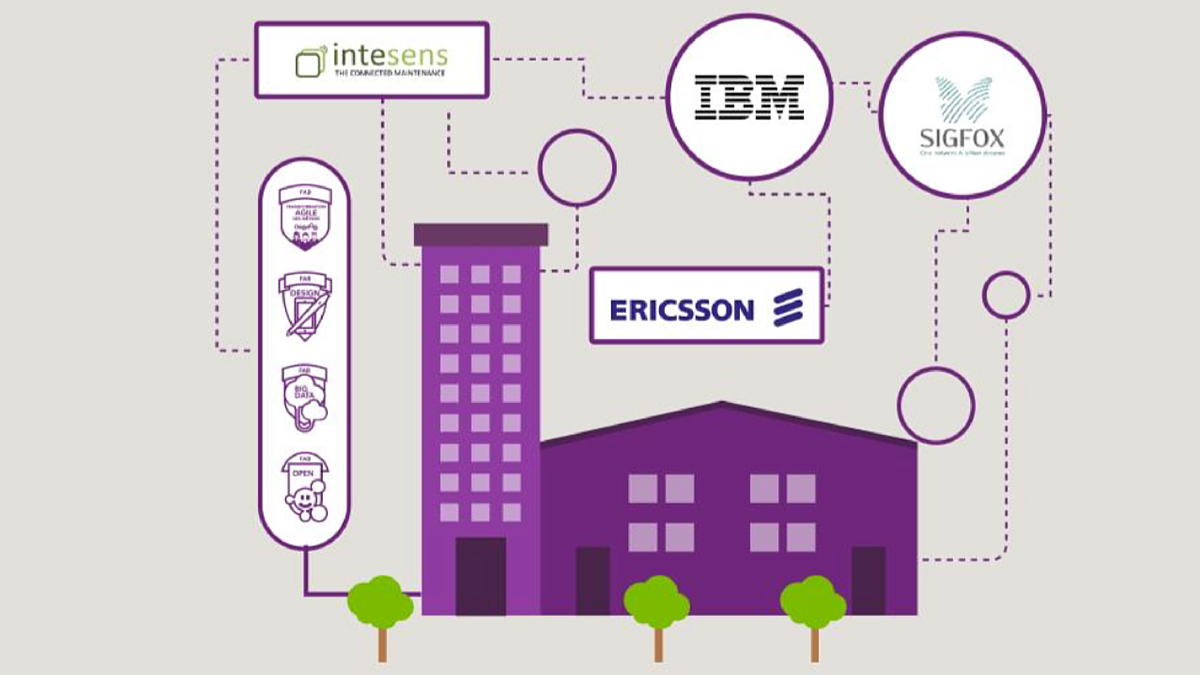
L’Internet des Objets (ou IoT pour _Internet of Things_), cet avatar du réseau des réseaux, est-il le prochain graal de la productivité ? Il redessine en tout cas le futur de l’industrie, au point qu’on évoque un nouveau jalon des révolutions industrielles, « l’Industrie 4.0 ». En plus de l’inévitable transformation digitale, les grands groupes industriels cherchent désormais à gagner la tête du peloton en bâtissant des usines “intelligentes” : des capteurs connectés au _cloud_, en passant par le traitement des données – le Big Data -,la digitalisation de l’industrie doit permettre de générer un flux d’informations intelligent pour une bonne prise de décision.
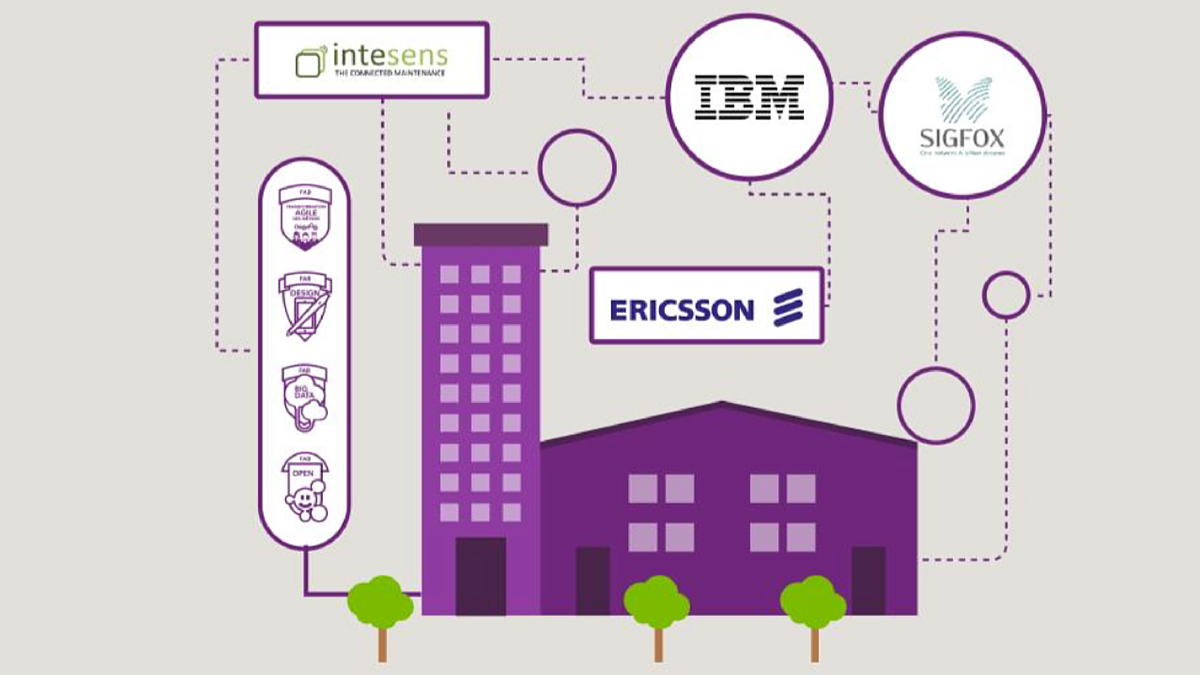
Vers la 4ème révolution industrielle ?
La première révolution industrielle, au XVIIIe siècle, fut celle du charbon et de la vapeur. La deuxième, à la fin du XIXe, celle de la fée électricité. Et on considère généralement que l’essor de l’informatique constitue, dans le courant de la deuxième moitié du XXe siècle et aux côtés de la maîtrise de l’atome une troisième étape de la révolution des modes de production.
Les prémisses d’une 4ème révolution se liraient dans l’avènement de l’Internet des Objets, cette collaboration d’éléments automatisés pour le contrôle d’entités physiques, rendant les outils de production « intelligents ». Cette nouvelle organisation permettrait de mieux servir les clients, en optimisant les ressources et en permettant une flexibilité accrue de la production.
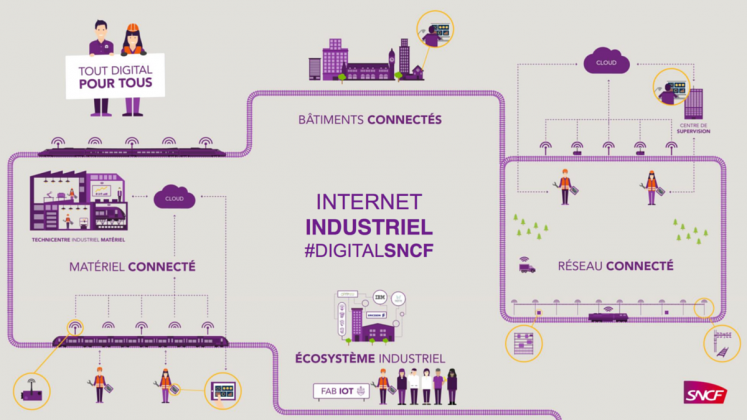
Sur quoi s’appuie cette « usine intelligente » ? D’abord sur la connectivité, une communication continue et instantanée entre les différents outils et postes de travail intégrés dans les chaînes de production et d’approvisionnement.
Pour cela, des capteurs installés sur les machines récoltent des données. Signe de l’émergence de l’IoT, le nombre d’objets connectés installés dans des sites de production devrait être multiplié par 4 d’ici 2020, soit 1 milliard d’objets, selon l’étude BI Intelligence. Le coût des capteurs a également été divisé par 7 au cours des 20 dernières années.
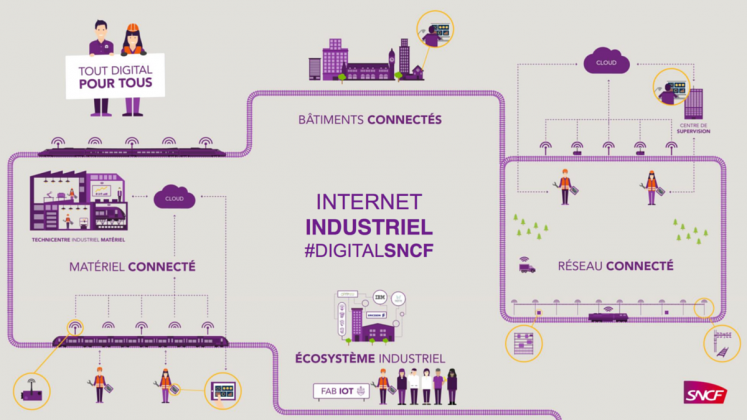
Les données et leur traitement, le _Big Data_, sont au cœur de l’usine du futur : cette dernière devient « _data-driven__ », _c’est-à-dire pilotée par la donnée, dans le cadre d’outils de simulation par exemple. La chaîne de production peut ainsi être modélisée et optimisée à partir de ces données, grâce à des tests virtuels. Il est aussi possible de former les ouvriers sans immobiliser l’outil de production.
Quels bénéfices ?
Repenser ainsi l’outil de production permettrait d’améliorer sa productivité, notamment en optimisant les _process_ industriels : on considère par exemple qu’il est ainsi possible de réduire de 30 à 50 % le temps d’immobilisation des machines ; tandis que les métiers techniques verraient leur productivité progresser de 40 à 55%…
Ainsi, General Electric monitore les données relatives aux anomalies de vibrations, de pression d’air et de température au sein de ses centrales électriques. Le système de traitement de ces données détecte automatiquement l’origine et la nature des problèmes, anticipe les pannes et recommande des interventions ciblées. Les gains de maintenance sont estimés entre 50 000 (dans le cas d’un changement de pièce) et 5 millions de dollars (en cas d’accident) pour chaque intervention.
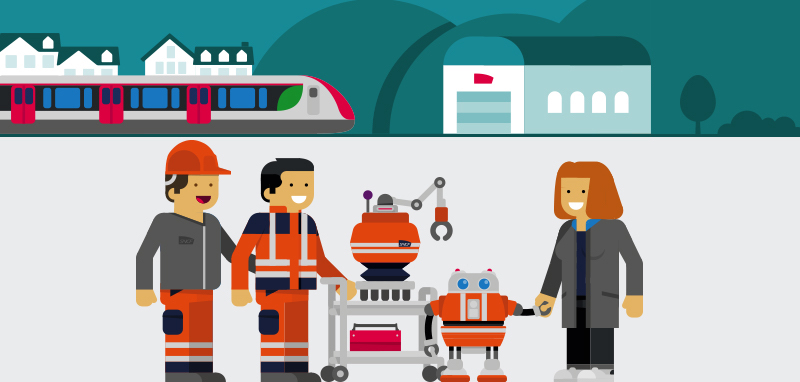